The $50,000 Safety Question?
Safety programs are an expense.
Their output is data that is presented for client review and for due diligence proof for audits/investigations/pre-qualifications.
Creation, implementation and maintenance of safety programs is a cost against the company’s bottom line.
So why do company safety programs receive little thought as to reducing the costs to maintain?
Does anyone rate how efficient their H&S program administration is?
How many safety teams analyze the costs and plan to reduce them through optimization of the workflows?
Answer: Not many. We convince ourselves that what we have works and that it’s always been done this way.
Most costs associated with programs are derived from the following 3 repeating workflows:
1. Onboarding-Assembling new worker certifications, orientation of workers, documentation review, signoffs and filing of documentation.
2. Administration-Constantly assembling, summarizing, and posting of field/operations data for internal and external reports.
3. Reporting-Weekly/Monthly/Annual reporting of KPI’s for internal stakeholders, clients, and prequalification platforms.
These three elements are found in every safety program and are areas that can be labelled “Busy Work”, where data is entered and re-entered, created and sent into information silos that must be revisited constantly to gather the fragmented pieces of information.
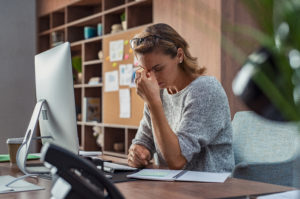
Working with fragmented, siloed information?
Why build a system like this and expect it to provide value to your operations?
When you look at your system elements, paper/digital platforms/mobile apps, how many times do you have to handle the same information? When your field data is on one platform, office systems on another (or several more), how much time is used every month to retrieve that data, re-enter/reformat (without errors) and generate reports for each stakeholder?
By planning and assembling a program that utilizes compatible elements, the workload to maintain these three pain points can be minimized. Don’t believe me? On a recent project I developed a system that had these results for one year:
• 13,500+ forms generated by field crews with 28,000+ signatures
• 7200+ certifications entered and monitored for expiry
• 700+ workers onboarded
• Weekly/Monthly generation of required reports
This was completed using one H&S administrator.
How was this possible:
1. Planning the workflows of all documents from creation to display.
2. Determining form types that would be utilized at every stage of the process.
3. Planning for KPI data inputs, Due Diligence or Data type.
4. Aligning of compatible platforms. Export capabilities are usually in .csv formats, but they must feed into preformatted locations in the receiving platform, or you’ve just created another copy that will have to be handled again.
The average annual cost for a H&S administrator is roughly $50,000. Most companies will experience turnover of H&S administrative staff or hire more staff to help run a HSMS without considering the “Root Cause” that got them in that position. Worker frustration; work overload due to broken processes; incompatible components in workflows???
This is magnified with project work as H&S admin. staff are brought together to meet the reporting requirements without having a structured format to implement. Photocopying/Scanning/E-mailing are the “components” of the system and must supply information to multiple personnel from the beginning.
What value are you getting for your $50,000?
Brandell Safety Consulting builds systems that provide an excellent ROI. Let’s talk!
0 Comments